Continuous Improvement
(Kaizen) Culture in Japan and in the West
→
Kaizen is a Japanese
workplace philosophy which focuses on making continuous small
improvements. Kaizen is constant. It is not a problem based
approach. Workers come up with new ideas and submit them all the
time, and quality circles meet frequently. Any hiccup on the factory
floor results in the meeting of a quality circle to talk about the
issue and discuss changes to implement. As a result, Japanese
companies are continuously becoming more efficient and streamlined,
allowing them to effectively
→
compete with other companies which also
integrate the
Kaizen
philosophy into their daily practice.
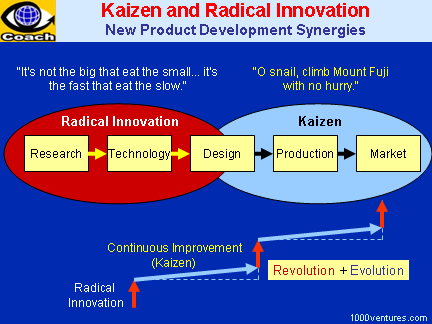
Many well known Japanese
companies such as
→
Toyota and
Canon use Kaizen, with a group approach
which includes everyone from
→
CEOs to janitors on the factory floor.
This group approach has been adopted successfully in other regions
of the world as well, but Japanese workers have refined it to an art
form. It is
Kaizen
mindset and process-oriented thinking, as opposed to the
result-oriented thinking favored by most Western firms, that has
enabled Japanese industry to attain its
→
competitive edge
in the world markets...
More
Suggestion Systems: American-style vs.
Japanese-style
The American-style suggestion system stresses
the suggestion's economic benefits and provides economic incentives.
The Japanese-style suggestion system stresses
the morale boosting benefits of positive employee participation...
More
* - the ability to introduce faster
new products and designs and respond quickly to changing customer demands; the
area in which Japanese companies maintain the largest competitive lead over US
and European firms |